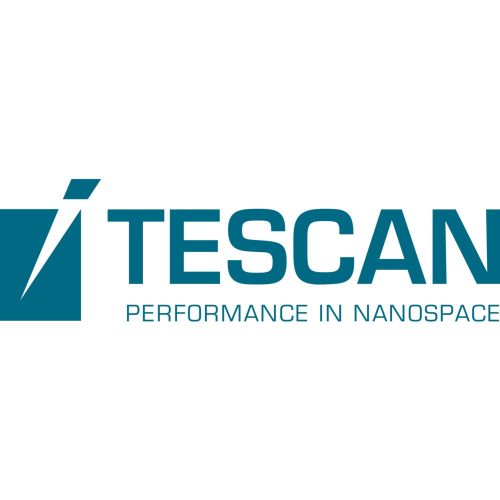
Join us at Interpore in New Orleans from May 14-17 to learn more about dynamic tomography.
Read moreIn the research project Smart*Light, a compact and bright X-ray source with tunable X-ray energy will be developed. To achieve this, a consortium of 12 partners in the Netherlands and Flanders has received 2.85M€ EFRO (European Regional Development Fund) funding. The Smart*Light X-ray source has the potential to be used in clinical diagnostics, state-of-the art research in materials sciences and the investigation of important artworks.
The XRE team welcomes Arno Merkle to the team, as our new Director of Business Development.
Come and visit us at SCA2017 in Vienna, Austria 28 August to 1 September 2017.
Read moreXRE will be present at ToScA 2017, an annual Tomography for Scientific Advancement symposium addressing hard and soft tissue imaging, understanding materials in 3D, recent advances in hardware and software, and a broad range of applications in tomography. Portsmouth, UK, 06 September 2017 - 08 September 2017.
Read moreToday we are delighted to announce XRE: A new alternative in 3D X-ray imaging, resulting from the merger of XRE and Inside Matters, two spin-offs from the Ghent University Centre for X-ray Tomography (UGCT).
At XRE, we are dedicated to offering dynamic solutions for your lab.
Zeelandia, one of the leading enterprises in the bread and bakery sector, joined forces to gain insights into the 3D structure of bread.
Read moreInnovative and lightweight composite materials are being used in the most demanding and challenging environments. Understanding and visualizing the internal structure of these composites in production and after intense usage is key to improve these high end materials. Early on detection of defects in production can help to finetune the production process and prevent potentially dramatic failure in the field. Monitoring the fatigue of the composite material during intense usage makes it possible to improve the design for the next generation of composites.
Read more